Corrugated boxes
production lines
INTEGRATED MODULAR SOLUTIONS FOR AUTOMATIC PRODUCTION OF CORRUGATED BOXES
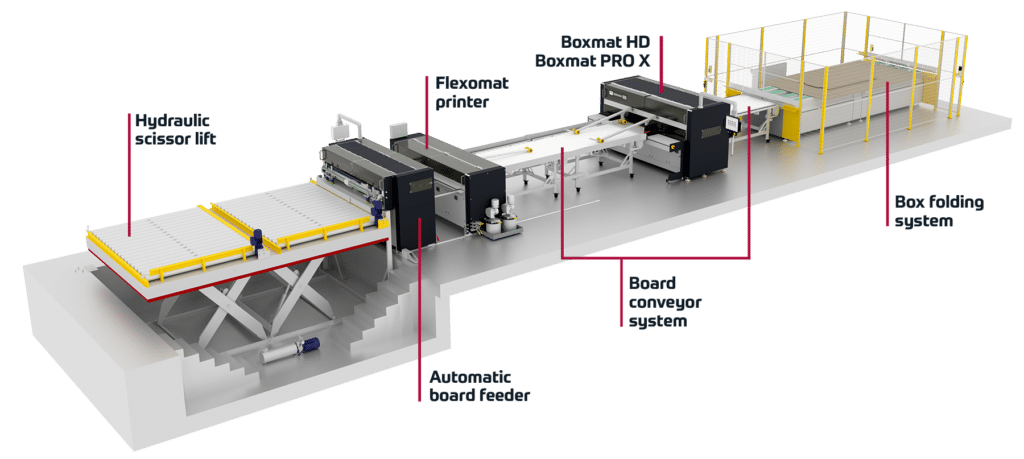
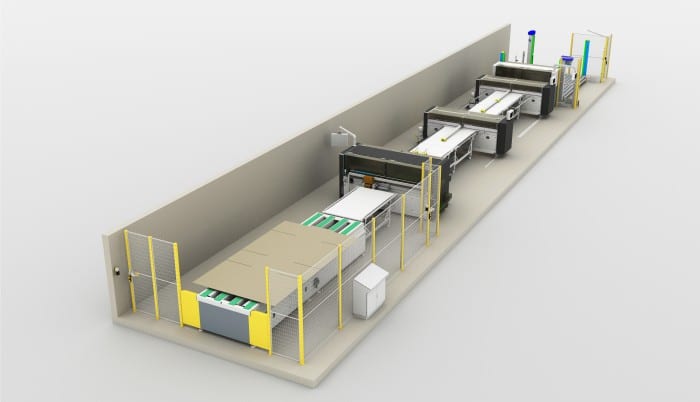

Automatic production lines for making of corrugated cardboard boxes made by Zemat Technology Group are designed and built as highly advanced systems with a wide range of automation and flexibility of configuration to provide the custom boxes manufacturing solution. Complete line may include synchronized lift, automatic feeder, flexographic printer, boxmaker machine with the gluing option, box folding unit and stacker.
All variants can be modified according to customer needs. The technical specification of each production line varies depending on the custom modifications.
- Board feeding
- Flexographic printing
- Automatic boxmaking
- Box folding
- Stacking
- Palletizing
From simple feed and cut, to much more complex feed - print - cut and crease - glue - fold and stack...
The whole box production process can be automated thanks to unique solutions provided by Boxmat series of machines.
THE BOXMAT AUTOMATIC PRODUCTION LINES ARE THE PERFECT SOLUTION FOR THE MOST DEMANDING CUSTOM BOX MANUFACTURING FACILITIES.
They can be implemented with shipping boxes or custom full color pre-printed boards for specialty packaging boxes.
Automatic BOXMAT systems save time and production cost, increase productivity in the boxmaking process
Industry 4.0 implementation with JQS Job Queue System
Smart scheduling of boxes production flow process Synchronized with any internal MRP, MES, ERP, MOM production control software
PRODUCTION LINE COMPONENTS:
1. HYDRAULIC SCISSOR LIFT WITH CONVEYOR
The LIFT design is adapted to the corrugated board stacks used by the customer.
Available stack parameters:
Length: 1500 – 5000 mm.
Width: up to 2400 mm.
Height: up to 1600 mm as standard. Individual configuration up to 1900 mm available.
The lift platform is built with a roller conveyor, positioning the stack of boards in the transverse axis and ensuring precise feed of boards into the machine.
There is an option to install the lift in the special trench/channel below the floor to work more conveniently with high stacks, or at the floor level on special rises and platforms.


2. AUTOMATIC BOARD FEEDER
Corrugated board FEEDER picks the boards from the stack using special manipulator and pneumatic suction cups and moved by swivel no-crash rolls. The boards are aligned by an automatic bumper to ensure a smooth transition to the next component of the production line. Technical parameters of the feeder are set according to the size of a stack of boards. Feeder is controlled by the HMI with a touch screen panel and synchronized with the full production line.


3. FLEXOGRAPHIC PRINTER

- Single or double printing cylinders
- 1 or 2 color printing (SIDE BY SIDE)
- Ceramic Anilox cylinder
- Print width: up to 760 mm (30”) – single cylinder
- Working print area width: 2400 mm (94”)
- Independent drives and motion control of each cylinder
- Repeat Rotation of flexo print cylinders
- Repeat Rotation of flexo print cylinders
- Special design steel/AL profile structure for vibration free printing
- No need for special tooling or dies
- Easy access for clean up and quick changeover of polymer plates
- Intuitive touch screen HMI for easy setup and control


4. BOARD CONVEYOR SYSTEM
Conveyor enables the transport of boards between the components of the production line and it is also a time buffer ensuring optimal and fast operation of the entire line.
The size of the conveyors depends on the size of used corrugated boards. The system is usually installed in the two places of the production line:
– between the printer and the boxmaker
– between the boxmaker and the automatic box folding system


5. BOXMAKER: BOXMAT HD / BOXMAT PROi
FEATURES:
- One pass operation to make a perfect box
- Several dozens of preprogrammed FFECO styles
- Switchover time – less than 60 seconds
- Large 19” touch screen HMI + INTELIGO System
- External board length control
- 10 sectional slotting knives
- Built-in VPN secure connection for HMI allowing remote diagnostics and updates
- No need for special tooling or dies
- Additional modules or equipment available
ONLY IN BOXMAT HD:
- Independent drive for each tool nest provides very fast position setup
- Integrated double die cutting system
- Counter-knife and counter scoring/creasing system
- Automatic recognition of the specific tool in the nest
- Conveyor waste/scrap REMOVAL system


6. BOXES FOLDING SYSTEM
The cut boxes are folded with the use of carriers placed on pneumatic actuators. It is most often used to make boxes from the FEFCO 2xx and 5xx series with glue already applied at the previous stage of production. The length of the supported formats can be up to 4200 mm and the width up to 2400 mm.

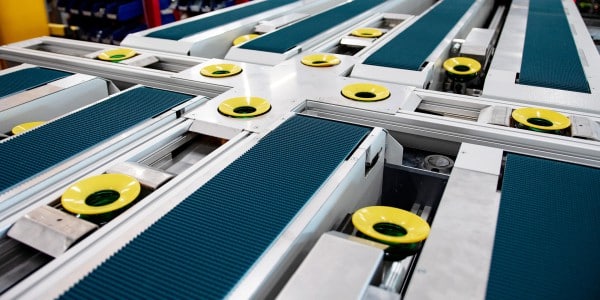
7. STACKER
Optional boxes stacking unit.

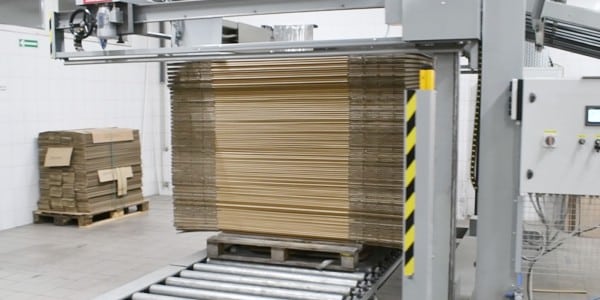
No LONG TERM corrugated board contracts!
With Boxmat machines, you have a freedom to choose your own
corrugated supplier and make your own BOXES ON DEMAND